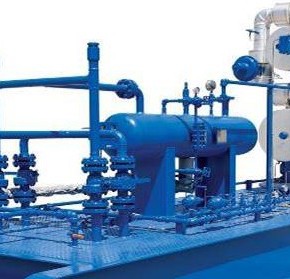
Posted on: 02. 12. 25
At Pro-Gas LLC in Dallas, we get that maximizing efficiency in Natural Gas Liquid (NGL) production is crucial for success in today’s competitive energy market. NGLs, valuable byproducts of natural gas processing, represent a significant revenue stream for producers. Optimizing NGL recovery not only boosts profitability but also contributes to resource conservation.
Let’s look at some strategies and technologies for maximizing efficiency in NGL production, from advanced separation techniques to energy optimization and process control.
Understanding the Importance of NGL Recovery
NGLs, including ethane, propane, butane, and pentanes, are valuable hydrocarbons found in natural gas streams. Their extraction is crucial for several reasons. First, they are valuable commodities used as feedstock in petrochemical plants and as fuel sources. Second, removing NGLs from natural gas ensures that the gas meets pipeline specifications and avoids issues like condensation and two-phase flow. Finally, maximizing NGL recovery contributes to resource utilization and reduces waste.
Advanced Separation Technologies for NGL Production
Several advanced separation technologies are employed to maximize NGL recovery. These include:
- Cryogenic Processing: This method uses extremely low temperatures to condense and separate NGLs from natural gas.6 It offers high recovery rates, especially for lighter hydrocarbons like ethane.7
- Lean Oil Absorption: This traditional method uses a lean oil to absorb NGLs from the gas stream.8 The NGL-rich oil is then stripped, and the NGLs are recovered.
- Membrane Separation: This technology utilizes specialized membranes to selectively separate NGLs from natural gas. It offers advantages in terms of energy efficiency and footprint.
- Adsorption: This process uses Temperature Swing Adsorption (TSA) and Pressure Swing Adsorption (PSA) are common techniques used.
Optimizing Process Parameters for NGL Recovery
Several process parameters can be optimized to enhance NGL recovery. These include:
- Temperature and Pressure: Careful control of temperature and pressure within the separation unit is critical for maximizing NGL condensation and separation.
- Flow Rate: Optimizing the flow rate of natural gas through the processing unit ensures adequate contact time for separation while minimizing pressure drop.
- Composition Analysis: Real-time analysis of the natural gas composition allows for adjustments in process parameters to maintain optimal recovery rates.
Energy Efficiency in NGL Production
Energy efficiency is a critical consideration in NGL production. Implementing energy-saving measures not only reduces operating costs but also minimizes environmental impact. Some strategies for enhancing energy efficiency include:
- Heat Integration: Recovering and reusing heat within the process can significantly reduce energy consumption.
- Waste Heat Recovery: Utilizing waste heat from other processes or equipment can further improve energy efficiency.
- Optimized Equipment Design: Employing high-efficiency equipment, such as pumps and compressors, can minimize energy losses.
Process Control and Automation for NGL Production
Advanced process control and automation systems play a vital role in maximizing NGL recovery and ensuring stable operations. These systems enable:
- Real-time Monitoring: Continuous monitoring of process parameters allows for quick identification and correction of deviations.
- Automated Control: Automated control systems maintain optimal operating conditions, maximizing NGL recovery and minimizing energy consumption.
- Data Analysis: Historical data analysis can reveal trends and opportunities for further process optimization.
Future Trends in NGL Production
The future of NGL production is likely to be shaped by several trends, including:
- Increased focus on energy efficiency: As energy costs rise and environmental concerns grow, there will be a greater emphasis on developing and implementing energy-efficient NGL recovery technologies.
- Advancements in separation technologies: Continued research and development are likely to lead to more efficient and cost-effective separation technologies.
- Digitalization and automation: The increasing use of digital technologies and automation will further enhance process control and optimization in NGL production.
Call on Pro-Gas Today | Optimize Your NGL Production
Maximizing efficiency in NGL production is crucial for profitability and resource conservation. By employing advanced separation technologies, optimizing process parameters, enhancing energy efficiency, and implementing process control systems, producers can significantly improve NGL recovery rates and reduce operating costs. As the industry continues to evolve, embracing innovation and adopting new technologies will be essential for staying competitive and maximizing the value of NGLs.
Contact us today at Pro-Gas LLC in Dallas, Texas, to explore how our expertise and services can help you optimize your NGL production operations. We are committed to providing cutting-edge solutions that maximize efficiency, profitability, and sustainability.
FAQ: Maximizing Efficiency in Natural Gas Liquid (NGL) Production
Q: What are NGLs?
NGLs (Natural Gas Liquids) are valuable hydrocarbons, including ethane, propane, butane, and pentanes, found in natural gas streams.
Q: Why is NGL recovery important?
NGL recovery is important because NGLs are valuable commodities, their removal ensures natural gas meets pipeline specifications, and it contributes to resource utilization.
Q: What are some advanced separation technologies for NGL production?
Some advanced separation technologies include cryogenic processing, lean oil absorption, membrane separation, and adsorption.
Q: How can energy efficiency be improved in NGL production?
Energy efficiency can be improved through heat integration, waste heat recovery, and optimized equipment design.
Q: What role does process control and automation play in NGL production?
Process control and automation enable real-time monitoring, automated control, and data analysis for process optimization.