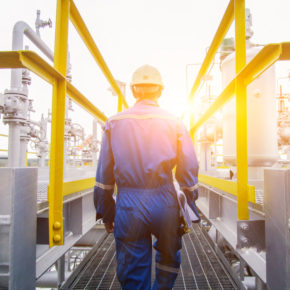
Posted on: 04. 15. 25
In the complexities of modern gas processing, maintaining the purity and integrity of natural gas streams is paramount. This is where filter separators come into play, serving as indispensable tools for removing contaminants and ensuring the delivery of high-quality gas. At Pro-Gas LLC, we understand the importance of reliable and efficient gas processing, and filter separators are a cornerstone of our operations.
Understanding Filter Separators
Filter separators are sophisticated devices designed to remove solid and liquid contaminants from gas streams. These contaminants, which can include dust, rust, pipe scale, water, and hydrocarbon liquids, can cause significant damage to downstream equipment, reduce efficiency, and compromise the quality of the final product.
Removal of Solid Contaminants
Filter separators utilize filtration elements to capture and remove solid particles from the gas stream. These elements, often made of pleated paper, fiberglass, or synthetic materials, are designed to trap particles of various sizes, preventing them from reaching downstream equipment. This ensures our gas streams are free from abrasive and potentially damaging solids, protecting our valuable equipment and extending its lifespan. The removal of these solids prevents damage to valves, compressors, and other sensitive components.
Separation of Liquid Contaminants
In addition to solid contaminants, gas streams often contain liquid droplets, such as water and hydrocarbon liquids. Filter separators employ centrifugal forces and coalescing elements to separate these liquids from the gas. Centrifugal forces cause the heavier liquid droplets to move outward and coalesce, forming larger droplets that can be easily removed. Coalescing elements — typically made of wire mesh or knitted fabric — enhance this process by providing a surface for liquid droplets to accumulate and grow. This process safeguards against corrosion and erosion in pipelines and processing equipment.
Protection of Downstream Equipment
By removing contaminants, filter separators play a crucial role in protecting downstream equipment, such as compressors, turbines, and pipelines. Contaminants can cause erosion, corrosion, and fouling, leading to costly repairs and downtime. By ensuring the purity of our gas streams, we minimize these risks and maintain the reliability of our operations. This protection leads to a longer lifespan of critical equipment.
Enhancement of Gas Quality
The removal of contaminants not only protects equipment but also enhances the quality of the final gas product. High-quality gas is essential for various applications, including power generation, industrial processes, and residential use. Filter separators ensure that the gas meets stringent quality standards, delivering clean and reliable energy to our customers. This enhanced quality increases the efficiency of combustion and reduces emissions.
Optimization of Process Efficiency
Clean gas streams contribute to the overall efficiency of gas processing operations. Contaminants can reduce the performance of downstream equipment, leading to increased energy consumption and reduced throughput. Filter separators help maintain optimal process conditions, ensuring that our operations run smoothly and efficiently. This optimization leads to reduced operational costs and increased profitability.
Benefits of Filter Separators in Gas Processing
Implementing filter separators in gas processing operations offers numerous benefits, including:
- Equipment Reliability: By removing contaminants, filter separators prevent damage to downstream equipment, ensuring reliable and continuous operation.
- Maintenance Costs: Clean gas streams minimize the need for equipment repairs and maintenance, leading to significant cost savings.
- Product Quality: Filter separators ensure that the gas meets stringent quality standards, delivering clean and reliable energy.
- Process Efficiency: Clean gas streams contribute to optimal process conditions, maximizing throughput and minimizing energy consumption.
- Environmental Protection: Removing contaminants reduces emissions and minimizes the environmental impact of gas processing operations.
Implementing Filter Separators in Your Operations
To effectively implement filter separators in your gas processing operations, consider the following steps:
- Assess Your Needs. Identify the specific contaminants present in your gas streams and determine the required filtration and separation efficiency.
- Select the Right System. Choose a filter separator system that meets your needs and integrates with your existing infrastructure.
- Proper Installation. Follow the manufacturer’s recommendations for installation to ensure optimal performance.
- Regular Maintenance. Establish a routine maintenance program to ensure the continued effectiveness of the filter separators.
- Monitor Performance. Regularly monitor the performance of the filter separators to identify any potential issues and optimize operations.
Filter separators are indispensable tools for modern gas processing, ensuring the purity and efficiency of our operations. By removing contaminants and protecting downstream equipment, they contribute to increased reliability, reduced maintenance costs, and improved product quality. At Pro-Gas LLC, we recognize the importance of filter separators in delivering clean and reliable energy to our customers.
Ready to optimize your gas processing operations with reliable filter separators? Reach out to Pro-Gas today for expert advice and solutions tailored to your specific needs.
FAQ
Q: What are filter separators?
A: Filter separators are devices designed to remove solid and liquid contaminants from gas streams, ensuring the purity and integrity of the gas.
Q: Why are filter separators important in gas processing?
A: They protect downstream equipment, enhance gas quality, optimize process efficiency, and reduce maintenance costs.
Q: How do filter separators remove contaminants?
A: They use filtration elements to remove solid particles and centrifugal forces and coalescing elements to separate liquid droplets.
Q: What are the benefits of using filter separators?
A: Increased equipment reliability, reduced maintenance costs, improved product quality, enhanced process efficiency, and environmental protection.
Q: How do I choose the right filter separator for my operations?
A: Assess your specific needs, select a system that integrates with your infrastructure, ensure proper installation, implement regular maintenance, and monitor performance.